Production Part Approval Process
Outsourced FAI and PPAP Improves Performance and Significantly Reduces Cost
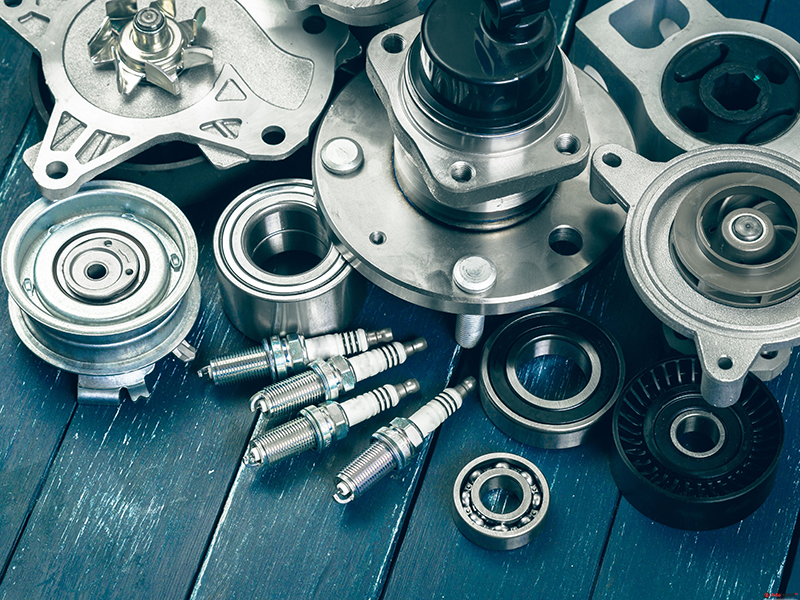
The Challenge
Our global aerospace actuation systems customer faced an ongoing backlog of supplier First Article Inspection Report (FAIR) validations and an increased internal demand for FAIR preparation. At the same time, they were faced with the strategic challenge to implement Production Part Approval Process (PPAP) across all critical suppliers.
To effectively manage this FAIR recovery and PPAP implementation program successfully, the customer also required a robust online platform to provide (1) real-time status of the validation process; (2) full visibility of supplier Right-First-Time (RFT) performance; and (3) access to details of key areas where suppliers were failing.
The Solution
The Results
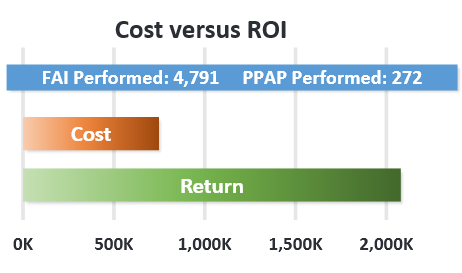
Our engagement with Verify has allowed us to realize significant cost savings. the Verify solution has improved visibility of FAl and PPAP approval status across our supply chain. ~ Aerospace Actuation Systems Customer