Supply Chain Disruptions – What we’ve learned forging ahead in 2023
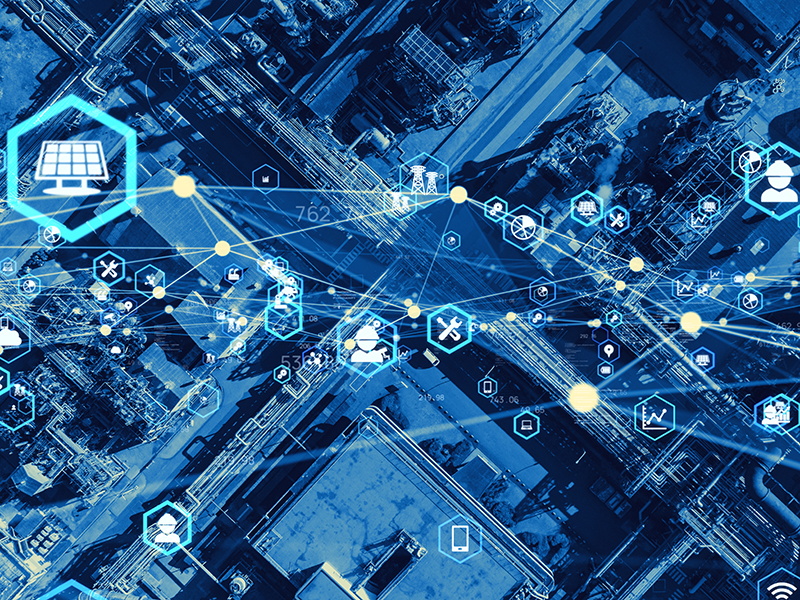
Looking forward through 2023 and beyond the A&D supply chain is certainly challenged some painful but insightful lessons from the after effects of the pandemic. The human capital landscape has evolved forcing a strategic shift in how we hire, develop and retain a productive workforce.
In addition to the pandemic, geopolitical events are escalating an already urgent need to assess and manage supply chain risk to new heights. The continued instability of material pricing and availability, coupled with an uncertain transportation landscape, are driving companies to transition from traditional reactive crisis management techniques toward more proactive and predictive resiliency models.
What is certain is that it will be a long time before smooth material supply can once again be taken for granted.
Verify, being entrenched in Supply Chain Risk Management, is increasingly engaged to provide risk solutions for not only our major customers but also working directly with their sub tiers and throughout the supply chain..
Our legacy position in Aerospace & Defense, as a direct provider of supply chain solutions to manage customer-supplier relationships, often provides broad optics into multi-tier challenges, from small business all the way up to the Major OEMs
Here are some key insights from the last year of providing rigorous boots on the ground risk assessments and SCRM technology to the Defense Industrial Base.
The after effects of the pandemic on lower tier suppliers is still not completely understood. Without robust high-level visibility into the lower tiers, organizations could be in the dark with respect to key components of their supply chain exposing unknown and costly vulnerabilities. How did these lower tier critical suppliers weather the aftermath of the pandemic? Supply chain disruptions have become a growing concern.
Most Organizations are still working their pre-pandemic paradigm — in silos and, the level of sophisticated strategic collaboration needed for recovery are still being talked about but not implemented. We continue to see attempts at mitigating risk being negated by traditional procurement buying at the lowest cost instead of working collaboratively to properly vet, review & understand the impact of this dated approach. If a supplier provides a quote where careful analysis of costs and schedules have been impacted by inflation, and that pricing is negatively affected, Customers are ready to move to another source instead of fixing what can be fixed. Moving serially from supplier to supplier based on cost alone will surely lead to disruptions if risk attributes are not visible and considered. The departments that are directly affected by specific risk attributes like IT and HR for example need to be a part of collaborative effort to meet the needs of an ever evolving supply chain. Limited surge capacity needs to be addressed at the strategic level, with clear direction to all stakeholders that the viability of a successful supply chain requires new methodology.
Regulations and compliance are growing exponentially as a response to global supply chain disruptions but without true consideration of the costs passed down to the suppliers. Unrealistic expenses for compliance on ESG and CMMC present real challenges, especially for those DIB suppliers in the 5th and 6th tiers. OEM’s need a broad strategy not only for assessing these suppliers but also anticipating the effects of non-compliance.
Congress is advocating for the health and welfare of these companies, OEM’s need to be partners in this effort to help them remain in the supply chain. Disenchantment with the growing compliance might lead to more suppliers exiting the sector all together.
Global conflicts affect raw materials, increasing price uncertainty. Take the nickel market for example, nickel stopped trading for the first time in London. Suppliers rely on global market pricing to execute their contracts. Geo-political conflicts are causing tenuous disruptions that move up and down the tiers, the need for true visibility is increasing.
Human resource challenges. The advent of many aging workers opting for early retirement against a new generation of workers who have nuanced expectations about their work environment and their future. It is apparent that few are choosing career paths in the technical fields.
People move more often, creating high turn-over rates. The marker for healthy turnover of under 5% is now 45 % and creates more stress on the remaining workforce, which equals more burnout.
What we’ve discovered with true risk visibility into human capital is that we need to take a good hard look at recruitment practices. Organizations need to look at in-house employee development. Increase focus on employee retention including upgrading and changing demographics, diversity & inclusion.
Risk attributes are becoming more granular requiring boots on the ground validation, cyber, capacity, local to supplier conditions. Being able to capture granular risk at the lower tiers of any complex supply chain will ensure resilience.
Risk resiliency assessments lead to a continuous improvement roadmap. It’s more than just mitigating risk, its about how we develop the critical suppliers who need help. But without that comprehensive supply chain intelligence, a strategic plan becomes untenable.
What these lessons are telling us is that we need to have a proactive approach to our supply chains that includes data and lots of it. Those organizations that truly analyze their current state and then use that data to proactively identify potential future disruptions will have a competitive advantage.
Contact us to learn more about our comprehensive supply chain risk resiliency tools.